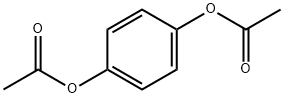
1,4-Diacetoxybenzene synthesis
- Product Name:1,4-Diacetoxybenzene
- CAS Number:1205-91-0
- Molecular formula:C10H10O4
- Molecular Weight:194.18

122-79-2
248 suppliers
$14.00/1g
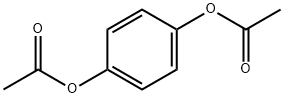
1205-91-0
178 suppliers
$12.00/5g
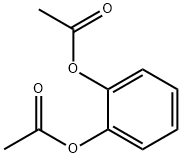
635-67-6
51 suppliers
$50.00/5 g
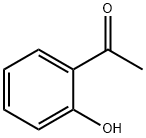
118-93-4
559 suppliers
$10.00/25g
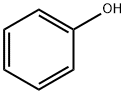
108-95-2
735 suppliers
$14.00/25g
Yield:-
Reaction Conditions:
HY-30 at 256; for 4 h;
Steps:
1. Catalysts tested The performance of various acidic catalysts in the rearrangement of PA to form 2-HAP were analyzed. Particular aspects studied were the orthoselectivity of the reaction, the production of by-products, and the total yields of 2-HAP. As reference catalysts, various types of zeolites were used, ones commonly used in the catalysis of reactions in gaseous phase, in acidic form or partially exchanged with Ga or La. The SiO2/Al2O3 ratio of the tested zeolites ranged between 25 and 120. More specific characteristics of these products are illustrated in the table below.The performance of these catalysts was compared to that of the catalysts T-4480 powder, T-4480 Extr. 1/16" and Ex-1720 Pt-1 belonging to the family of compounds described in the patent EP-A-369364.2. Laboratory microplant The catalytic tests were conducted in conditions of gas flow using a laboratory microplant. The plant may be divided into three main zones: (a) feed zone, (b) reaction zone, (c) zone of collection of products.A. FEED ZONE The flow of He is regulated by a mass flowmeter calibrated with a bubble flowmeter. The phenylacetate (PA) is supplied by an infusion pump and is introduced into the line heated at 200°C and controlled by an iron/Constantan thermocouple.B. REACTION ZONE The tubular reactor consists of a stainless steel tube with a section of 1 inch and a length of approximately 50 cm. Inside the tube, a perforated diaphragm blocks the catalyst inside the reactor, enabling the passage of the flow of gas. In contact with the tube are two electrically heated copper jaws controlled by means of a thermocouple. The ensemble is insulated by perlite and enclosed in a brass cylinder. Inserted in the catalytic bed is a 1/8-inch stainless steel tube inside which a mobile thermocouple can slide, thus enabling measurement of the reaction temperature at different heights of the catalytic bed. The gases coming out are maintained at 100°C by means of a resistor controlled by a thermoregulator to prevent crystallization of the heavier products.C. ZONE FOR COLLECTION OF PRODUCTS At output from the hot zone is set a glass crystallizer at room temperature that enables collection of the condensates. Subsequently, there are two bubble adsorbers containing acetone and set in ice (for the collection of the products that do not condense in the crystallizer) and a bubble adsorber containing absolute ethanol to transform the ketene that may possibly be formed in acetyl acetate.3. Conditions of reaction The experimental conditions are the ones that yielded the best results following upon a prior screening. These conditions were: Temperature of the incoming band = 200°C.Temperature at output from the reactor = 100°C.Reaction temperature (i.e., the temperature inside the reactor in the reaction zone) = 256°C.Temperature of the catalytic bed = 265°C.Activation of the catalyst: 5 hours at 300°C in He (60 ml/min).Feed: quantity of PA contained in the inert gas =10%.spatial velocity (WHSV) inside the reactor = 0.5 h-1.Pressure: atmospheric4. Results After 4 hours from the start of reaction, the reaction products were determined quantitatively via gas-chromatography analysis. The analyses yielded the following results: [Table 2] From the data given in Table 2 it may be noted that the traditional zeolites (specimens 1, 2 and 5-7) have a high 2-HAP / 4-HAP selectivity, but the yield in 2-HAP is quite modest in that a substantial proportion of PA is converted into phenol, as is evident from the low values of the 2-HAP/PhOH ratio. The doping of the zeolites with metals (see specimens 3, 4 and 6) does not improve the yield in 2-HAP, nor does it reduce the formation of the PhOH by-product. Instead, the catalysts according to the present invention (see specimens 8-10) revealed a high 2-HAP/4-HAP selectivity, together with a value of 2-HAP/PhOH ratio considerably higher than that obtained for any of the reference specimens. As emerges from the Table, the synergy between these two factors leads to 2-HAP yields that are surprisingly higher than those obtained from all the reference specimens. The yields in further by-products of reaction (2-AcPA, 4-AcPA) are lower than 0.2%. Further tests were carried out on a longer production cycle (4 hours/day for three days) to verify the persistence of activity and the constancy of the yields over time. During the entire duration of the test, none of the above-mentioned reference catalysts managed to exceed or even approach the yield values found in the process forming the subject of the invention. The persistence of high yield values over time for the process forming the subject of the invention enables retardation of the cycles of reactivation of the catalyst, thus increasing the productivity of the plants.
References:
ENDURA S.p.A. EP1220823, 2004, B1 Location in patent:Page 6-7

64-19-7
1551 suppliers
$10.00/25ML

123-31-9
836 suppliers
$13.00/25g
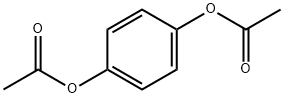
1205-91-0
178 suppliers
$12.00/5g
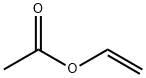
108-05-4
567 suppliers
$4.00/1000g

123-31-9
836 suppliers
$13.00/25g
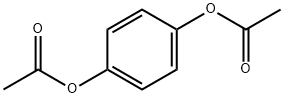
1205-91-0
178 suppliers
$12.00/5g

108-24-7
5 suppliers
$14.00/250ML

123-31-9
836 suppliers
$13.00/25g
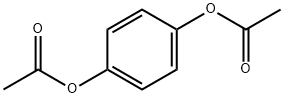
1205-91-0
178 suppliers
$12.00/5g
201230-82-2
1 suppliers
inquiry

150-76-5
767 suppliers
$5.00/5 g

74-88-4
348 suppliers
$15.00/10g
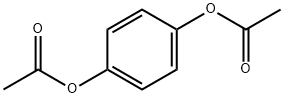
1205-91-0
178 suppliers
$12.00/5g