
VINYL CHLORIDE synthesis
- Product Name:VINYL CHLORIDE
- CAS Number:75-01-4
- Molecular formula:C2H3Cl
- Molecular Weight:62.5

107-06-2
431 suppliers
$14.00/25g

7647-01-0
11 suppliers
$10.00/10g

75-01-4
130 suppliers
$19.69/1mL
Yield:75-01-4 99.52%
Reaction Conditions:
at 450 - 550; under 10501.1 - 26252.6 Torr; for 0.00416667 - 0.00833333 h;
Steps:
According to an especially preferred form of implementation, 1, 2-DICHLOROETHANE is heated to almost boiling temperature in three stages, utilizing the energy content of the hot crack- ing gases and of the flue gases of the cracking furnace: - IN the second heat exchanger, which utilizes the waste heat of the quench column, liquid 1, 2-dichloroethane is heated to approximately 120-150°C by the saturated vapour mixture (mainly comprising vinyl chloride, hydrogen chloride and unreacted 1,2- DICHLOROETHANE) that leaves the quench column at the top, - IN the first heat exchanger (trimming heat exchanger = vapour-operated heat exchanger for pressure regulation and/or fine adjustment of the heat requirement in the EDC crack- ing), the liquid 1, 2-dichloroethane is further heated externally by steam, - IN a third heat exchanger in the convection zone of the cracking furnace, the 1,2-di- CHLOROETHANE, which is still liquid, is heated by the flue gases of the cracking furnace to 200-250°C. The 1, 2-dichloroethane which is still liquid after that 3-stage heating process is vaporized in an external, SO-CALLED"EDC VAPORIZER"USING the waste heat of the hot cracking gases having a temperature of 450-550°C issuing from the cracking furnace, under a pressure of from 1.4 to 3.5 MPa, preferably from 1.4 to 2.5 MPa and especially from 1.6 to 2.2 MPa. The then gaseous 1, 2-DICHLOROETHANE is passed into the radiation zone of the cracking furnace and heated to above 450°C within 5-10 seconds, preferably within 6-7 seconds. The energy supply to the cracking furnace is preferably distributed as follows : 1 st burner row (EDC entry): 30-70 % burner row (s) middle: 20-40 % last burner row (cracking gas exit): 10-20 % The total residence time of the EDC in the radiation zone of the cracking furnace should be 15-30 seconds, preferably 18-23 seconds. The hot cracking gas having a temperature of from 450°C to 550°C is passed through the external EDC vaporizer and thereafter is cooled to saturated vapour temperature in the quench column by direct cooling with A liquid mixture of 1, 2-dichloroethane, vinyl chloride and dissolved hydrogen chloride. The pressure in the quench column is 1.4-2 MPa, preferably 1.5-1. 7 MPa. The top stream of the quench is advantageously used for pre-heating liquid 1, 2-dichloro- ethane and is then cooled to 50-60°C with cooling water or by means of air coolers. The gas stream and the liquid stream from the quench system are then fed for distillation to separate hydrogen chloride, vinyl chloride and unreacted 1, 2-dichloroethane. In the first stage, hydrogen chloride is separated from vinyl chloride and 1, 2-dichloroethane over the top of the column. Owing to the quench pressure of 1.5-1. 7 MPa, the first distillation column is operated at 1.2 MPa AND-25°C in the top. In the upper portion of the convection zone of the cracking furnace, steam can be obtained and/or the combustion air for the cracking furnace can be pre-heated, while the flue gases are simultaneously cooled. Surprisingly, it has been found that adherence to specific operating parameters, especially a pressure in the cracking coil of 1.6-1. 9 MPa, to rapid heating of the 1, 2-dichloroethane in the first portion of the radiation zone and adherence to the above-described residence times AND/OR specific firing in the individual cracking furnace segments drastically reduce the formation of by-products and at the same time prolong the operating time of the furnace. The refrigeration output required to liquefy the return material is, by virtue of the pressure in the first distillation column, only 35.4 kW/t of target product. The EDC yield obtained (yield of vinyl chloride based on reacted pure 1, 2-DICHLOROETHANE) according to the described process is 99.5 %. Owing to the high entry temperature of the 1, 2-DICHLOROETHANE into the radiation zone of the cracking furnace the consumption of primary energy in the cracking furnace is also very low in comparison with other, known processes. The following Table shows the invention in comparison with the prior art DE 34 40 685 and EP 0 264 065 discussed in the introduction. Table : EVALUATION OF THE TEST RESULTS according to the similarly to similarly to invention DE 34 40 685 EP 0 264 065 formation of by-products 11 17 10 in kg per tonne of target product 1, 2-dichloroethane yield in 99. 52 99. 3 99. 54 % by weight total energy consumption 904 890 943 of EDC cracking in kW/t of vinyl chloride energy consumption of 201 (by cracking 210 (by cracking 235 (by steam) EDC vaporization in kW/t gas) gas) of vinyl chloride furnace operating time 19 10 20 between cleaning periods in months according to the similarly to similarly to invention DE 34 40 685 EP 0 264 065 refrigeration output for 35.4 33.7 92.5 liquefying the hydrogen chloride at the top of the HO column in kW/t of target product Definitions: formation of by-products = the sum of all the by-products resulting in the cracking of 1, 2-dichloroethane 1, 2-DICHLOROETHANE YIELD = yield of vinyl chloride based on the pure, reacted 1, 2-DICHLOROETHANE total energy consumption : total primary energy used in the cracking furnace (tube reactor) in the form of heating gas or heating oil energy consumption of EDC vaporization: energy used to heat 1, 2-DICHLOROETHANE in the EDC vaporizer to boiling temperature and FOR THE TOTAL VAPORIZATION OF the 1, 2- dichloroethane stream to the cracking furnace (tube reactor) ; in the case of the high- pressure cracking and the invention that energy is extracted from the cracking gas after it leaves the tube reactor, in the case of the low-pressure cracking that energy is supplied externally by means of steam. furnace operating time = the time after which the reaction has to be discontinued in order to clean the cracking furnace (tube reactor). refrigeration output for liquefying hydrogen chloride in the HCI column = the electrical energy that has to be used to generate cold in order to condense the quantity of hydrogen chloride required as return material in the first distillation column (HCI column).
References:
WO2004/89860,2004,A1 Location in patent:Page 3-6

75-34-3
106 suppliers
$22.69/48602

75-01-4
130 suppliers
$19.69/1mL
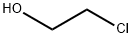
107-07-3
3 suppliers
$21.53/50ml

75-01-4
130 suppliers
$19.69/1mL

75-34-3
106 suppliers
$22.69/48602

75-01-4
130 suppliers
$19.69/1mL

79-00-5
206 suppliers
$15.00/10ml
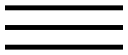
74-86-2
73 suppliers
inquiry

75-01-4
130 suppliers
$19.69/1mL