Identification | Back Directory | [Name]
POLY(ETHYLENE TEREPHTHALATE) | [CAS]
25038-59-9 | [Synonyms]
Mylar Terom Vituf Estar klt40 KLT 40 Dowlex Amilar fiberv Terfan Tergal mylara mylarc mylart Lavsan Mylar T mylarhs Mylar A Mylar C Melinex arnitea arniteg Terphan vfr3801 Fiber V Celanar Clertuf Cleartuf Arnite G Arnite A Estrofol Lumirror Iambolen Ertalyte Hostadur VFR 3801 Meliform Mylar hs melinexo mylarc-25 Petra 130 Petra 230 Petra 242 Melinex O estrofolb scotchpar Superfloc Impet 330 hostadurk Hostaphan daiyafoil hostadura PET FIBER Lawsonite lumilar100 Daiya foil RTP 1105FR Scotch par estrofolow Estrofol B Valox 9215 Hostadur A Hostadur K Mylar C-25 arniteg600 arnitea200 Pegoterate Petra 130FR arnitefp800 lumirror38s Estrofol Ow crastins330 crastins350 crastins440 hostaphanrn Kodapak PET Lumilar 100 Lumirror 38S Hostaphan rn hostaphanbnh Arnite A 200 Arnite G 600 cassappretsr nitronlavsan Nitron lavsan Cassappret sr Grilpet EV-30 Arnite fp 800 Kodapak 5214A Crastin S 330 Crastin S 350 Crastin S 440 Hostaphan bnh arnitea-049000 polyester chip Tenite PET 9902 ARNITE A-049000 Cleartuf Series hostadurk-vp4022 Ultralen SP 3705 Polyestergranular nitron(polyester) Crastine XMB 1068 Copolyester 13339 Traytuf ultra-clea Ultralen SP 3700 S Hostadur K-vp 4022 Traytuf ultra-clear Celstran PETG30-01-4 e20(japanesepolyester) Electrafil J-1800/CF/30 Kodar PETG copolyester 6763 Advanite23001PolyesterChips POLY(ETHYLENE TEREPHTHALATE) ethyleneterephthalatepolymer polyethyleneterephthalatefilm Kodapak PET copolyester 13339 Ethylene terephthalate polymer Polyethylene terephthalate film Mitsubishi kasei GF-PET 6010G15 Poly(oxyethyleneoxyterephthaloyl) POLY(ETHYLENE GLYCOL TEREPHTHALATE) Compound fibre of polyester and nylon PET RESIN / POYESTER CHIPS BOTTLE GRADE Poly(oxy-1,2-ethanediyloxycarbonyl-1,4- terephtahlicacid-ethyleneglycolpolyester poly(ethylene terephthalate) macromolecule (3 Strips) Polyethylene Terephthalate (PET) Polyethylene Terephthalate (PET) (3 Strips) Terephtahlic acid-ethylene glycol polyester Poly(ethylene terephthalate), White granular Poly(ethylene terephthalate) 8,000 or 50,000 Polyethylene Terephthalate ISO 9001:2015 REACH Polyethyleneglycolterephthalateresin(PETF-61-BR) Polyethylene Terephthalate (PET) WK-881 for CSD grade 1,4-Benzenedicarboxylic acid, polymer with 1,2-ethanediol Poly(oxy-1,2-ethanediyloxycarbonyl-1,4-phenylenecarbonyl) POLY(ETHYLENE TEREPHTHALATE) (RYNITE 530 POLYESTER RESIN) POLY(ETHYLENE TEREPHTHALATE) (RYNITE FR5 30 POLYESTER RESIN) Polyethylene Terephthalate (PET) WK-811 for hot filled grade Polyethylene Terephthalate (PET) WK-821 for oil bottle grade Polyethylene Terephthalate (PET) WK-801 for water bottle grade Indium tin oxide coated PET,Polyethylene terephthalate film, ITO coated Polyethylene Terephthalate, (contains 30% glass particles as reinforcer) 3DXNANO ESD CNT-PETG carbon nanotube reinforced polyethylene terephthalate glycol copolymer 3D printing filament 3DXNANO(TM) ESD CNT-PETG carbon nanotube reinforced polyethylene terephthalate glycol copolymer 3D printing filament 3DXNANO(TM) ESD CNT-PETG carbon nanotube reinforced polyethylene terephthalate glycol copolymer 3D printing filament black, diam. 1.75 mm 3DXNANO(TM) ESD CNT-PETG carbon nanotube reinforced polyethylene terephthalate glycol copolymer 3D printing filament black, diam. 2.85 mm | [Molecular Formula]
(C10H8O4)n | [MDL Number]
MFCD00084422 | [MOL File]
25038-59-9.mol | [Molecular Weight]
228.199 |
Chemical Properties | Back Directory | [Melting point ]
250-255 °C
| [Boiling point ]
>170 °C(Press: 10 Torr) | [density ]
1.68 g/mL at 25 °C
| [refractive index ]
1.5750 | [storage temp. ]
Room Temperature | [form ]
pellets
| [color ]
black | [Odor]
Odorless | [InChI]
InChI=1S/C8H6O4.C2H6O2/c9-7(10)5-1-2-6(4-3-5)8(11)12;3-1-2-4/h1-4H,(H,9,10)(H,11,12);3-4H,1-2H2 | [InChIKey]
FYIBGDKNYYMMAG-UHFFFAOYSA-N | [SMILES]
O([H])C(C1C([H])=C([H])C(C(=O)O[H])=C([H])C=1[H])=O.O([H])C([H])([H])C([H])([H])O[H] | [Uses]
The first stage to produce Polyethylene Terephthalate (PET) is the reaction of ethylene glycol with terephthalic acid or dimethyl terephthalate. After the initial reaction, two or three polymerization steps are then performed, depending on the required molecular weight. The chemical structure of PET is composed of repeated units. Each unit has a physical length of about 1.09 nm and a molecular weight of ~200. PET monomer consists from an aromatic ring coupled with a short aliphatic chain that makes PET a stiff molecule as compared to other aliphatic polymers such as polyolefin or polyamide. The lack of segmental mobility in the polymer chains results in relatively high thermal stability. A textile grade polymer will have an average number of 100 repeat units per molecule so that the extended length of the typical polymer chain is about 100 nm with a molecular weight of ~20,000. Higher levels of polymerization produce higher strength fibers but the melt viscosity and stability of the melt to even tiny amounts of moisture causes hydrolytic degradation. Photo-degradation of PET occurs after exposure to near-ultraviolet light resulting in either chain scission by Norrish I and II reactions. Cross-linking also takes place and polymer becomes brittle, discolored, and with uneven surface. PET when exposed to UV light degrades rather rapidly leading to deterioration in physical and mechanical properties and develops intense yellow color. It has been suggested that the photo-oxidation of PET involves the formation of hydroperoxide species through oxidation of the CH2 groups adjacent to the ester linkages and the hydroperoxide species involving the formation of photoproducts through several pathways. The ester moieties in the terephthalate moiety as well as CH2 groups are strongly involved in the photo-degradation of PET. The vinyl ester ends also act as cross-linkers and gelling agents. They polymerize and the polymers thermally degrade to give yellow or brown polyenes that discolor the final polymer. The formation of highly conjugated species is catalyzed by carboxyl groups. The formation of colored species is followed by increase of more carboxyl terminated species. Hence, the product having higher carboxyl value is subject to more discoloration. Furthermore, as the carboxyl content increases, the thermo-oxidative stability decreases. The carboxyl end groups act as catalysts for further degradation. | [EPA Substance Registry System]
Poly(ethylene terephthalate) (25038-59-9) |
Hazard Information | Back Directory | [Definition]
ChEBI: A macromolecule composed of repeating ethylene terephthalate units. | [Description]
Polyethylene terephthalate (PET) is a saturated thermoplastic polyester. The first PET fibers, DacronTM and TeryleneTM, were first developed by Whinfield and Dixon in England. The first DacronTM plant began production in 1953. PET is produced using direct polycondensation reaction with ethylene glycol and terephthalic acid.lt is widely used in synthetic fibers which simulate wool, cotton, or rayon. PET films MylarTM, MelinexTM) are biaxially oriented by cold stretching the extruded sheets in two directions. This increases the crystallinity and reduces the tendency to shrink when heated. PET films are used in capacitors,slot liners for motors,magnetic tape, x-ray film, photographic film, graphic art and drafting applications,and food packaging such as boil-in-bags. | [Chemical Properties]
Polyethylene terephthalate (PET) is a semi crystalline polymer possessing excellent chemical resistance, melt mobility and spinnability. The polymer is composed of repeating units as shown in the Figure 1. Each unit having a physical length of about 1.09 nm and a molecular weight of ~200. When it is produced from the reaction of terephthalic acid and ethylene glycol, it is capped on the left by H- and the right by –OH. Polymerization is thus accompanied by the production of water which is removed under elevated temperature and vacuum. Accordingly the presence of water in the molten state will rapidly depolymerize the structure so that thorough drying of the polymer prior to melt spinning of fibers is necessary.
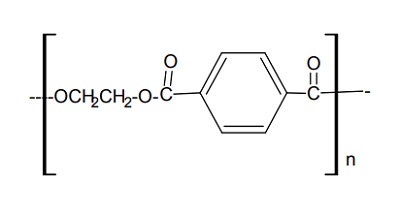
The aromatic ring coupled with short aliphatic chain makes the polymer a stiff molecule as compared to other aliphatic polymers such as polyolefin or polyamide. The lack of segmental mobility in the polymer chains results in relatively high thermal stability. A textile grade polymer will have an average number of 100 repeat units per molecule so that the extended length of the typical polymer chain is about 100nm with a molecular weight about 20,000. Higher levels of polymerization produces higher strength fibers but the melt viscosity and stability of the melt to even tiny amounts of moisture causes hydrolytic degradation. The measurement of average degree of polymerization is done either by molten viscosity (by measuring the pressure drop through a calibrated orifice) or the viscosity of the diluted polymer in an appropriate solvent. The latter is measure of polymer chain length known as Intrinsic viscosity or IV and the value for a typical fiber grade polymer is 0.6 dl/g in 60/40 w/w mixture of phenol and tetrachloroethane solvent. The IV in the latter solvent is related to Mv (Viscosity average molecular weight) of the polymer by the Mark Howink equation (Equation 1). | [Preparation]
Poly(ethylene terephthalate) is prepared by the reaction of either terephthalic acid or dimethyl terephthalate with ethylene glycol, and its repeating unit has the general structure
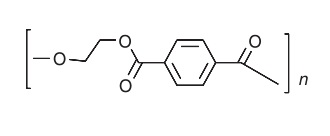
The resin has the ability to be oriented by a drawing process and crystallized to yield a high-strength product. | [General Description]
Made using premium Eastman PETG + Multi-wall Carbon Nanotubes (CNTs). 3DXNano? CNT enchanced compounds are used in critical applications that require electrostatic discharge(ESD) protection and a high level of cleanliness. Manufatuered with consistency in mind-3DXTech uses a proprietary formulation of virgin Eastman PETG (Polyethylene Terephtalate Glycol Copolymer) resin; multi-wall carbon nanotubes; and process/dispersion modifiers in order to give you the best possible printing experience.
Benefits of PETG include:
- Superior Chemical Resistance vs. ABS
- Amorphous: Low and near isotropic shrinkage
- Low moisture absorption: 3x lower vs. ABS
- Very low odor emitted during printing
- Superior ductility vs. ABS
- Wide processing range: 230 - 270 °C
Benefits of CNTs include:
- Consistent surface resistivity
- low additive loading rates
- Improved retention of impact & elongation
- Low particulate contamination
- Minimal contribution to outgassing and ionic contamination
| [Synthesis]
The synthesis of PET begins with the esterification of either terephthalic acid or dimethyl terephthalate with ethylene glycol, yielding bis(hydroxyethyl)terephthalate (BHET). The BHET is then polymerized up to about 30 repeat units (Awaja and Pavel 2005). Next, to achieve a degree of polymerization (DP) of about 100 repeat units, polycondensation is performed at temperatures > 270°C and pressures > 50 Pa (Ravindranath and Mashelkar 1986). To produce bottle-grade PET, the DP must be > 150 repeat units, which is typically accomplished via solidstate polymerization, a process that requires temperatures > 200°C, pressures > 100 Pa, and incubation times of at least 15 hr (Al-Ghatta et al. 1997).
It is becoming increasingly common for manufacturers to market copolymers for purposes previously filled by homopolymer PET. Copolymer blends, such as polybutylene terephthalate/PET, have certain advantages over homopolymer PET with regard to mechanical properties and resistance to degradation (Grossetête et al. 2000; GuerricaEchevarría and Eguiazábal 2009). In the United States, a clear plastic bottle may be made with copolymers and still be legally marketed as PET, according to applicable federal regulations [e.g., 21 CFR §177.1630 (U.S. Food and Drug Administration 2009). |
|
|